Creado por estudiantes de Ingenieria Agroindustrial de la Universidad Popular Del Cesar. (COLOMBIA)
Translate
viernes, 29 de noviembre de 2013
BIORREACTORES Y
UNIDADES DE FERMENTACIÓN
Los procesos de cultivo y propagación, entre los cuales se encuentra la
Fermentación, requieren un control exhaustivo de las condiciones higiénicas y
las variables del Proceso. Cualquier agente incontrolado puede suponer la
pérdida de las horas, o incluso los días necesarios para obtener un lote de
producto.
Los procesos de fermentación implican frecuentemente tiempos de fabricación
considerables, desde unas pocas horas hasta varios días en función del producto
y el lote a procesar. Este factor crítico de la programación de la producción
unido a que, a menudo, los productos en el interior de los tanques de
fermentación son excelentes caldos de cultivo para cualquier microorganismo,
hace que las condiciones de diseño y la operativa del sistema de control cobren
especial importancia

Desde la zona de tratamiento térmico hasta el envío a la siguiente etapa
del proceso, pasando por el diseño de los tanques y sus distintos sistemas de
agitación, acondicionamiento térmico, atmósfera inerte, seguridad alimentaria y
esterilización, GEA Process Engineering Spain le propone una solución global
completamente integrada en su proceso, de forma que no exista ningún factor
incontrolado que pueda hacer peligrar su producción.

Flexibilizamos las unidades de Fermentación haciendo que los tanques puedan
ser compartidos con otras partes del proceso, funcionando alternativamente como
tanques de mezcla o tanques de almacenamiento intermedio de producto final
antes de la fase de envasado. A fin de cuentas todos comparten un condicionante
común: su diseño higiénico ultralimpio o aséptico, y cuentan con la garantía
que aporta un Sistema de Control fiable y enfocado a la gestión de la seguridad
alimentaria.

jueves, 28 de noviembre de 2013
SOLUCIONES AL AGUA :
BIORREACTORES DE MEMBRANA
Las membranas de ultra-filtración son sencillamente un filtro con un tamaño de poro extremadamente pequeño, lo que permite separar el agua de los contaminantes disueltos de una manera muy efectiva.
Un aspecto fundamental del diseño es el empleo e un mecanismo difusor de aire situado bajo las membranas. Este mecanismo genera una columna de burbujas que atraviesa el módulo de las membranas limpiándolas.
Este equipo de filtrado puede utilizarse en los reactores biológicos con membrana de ultra-filtración (MBR), los sistemas tecnológicos más avanzados de depuración de aguas residuales.
FOTOBIORREACTOR
Un
fotobiorreactor es un bioreactor que incorpora algún tipo de fuente de luz.
Prácticamente cualquier recipiente translúcido que se podría llamar un PBR, sin
embargo, el término se utiliza más comúnmente para definir un sistema cerrado,
en contraposición a un tanque abierto o estanque. Fotobiorreactores son
utilizadas para el cultivo de pequeños organismos fototróficas como las
cianobacterias, algas o plantas de musgo. Estos organismos utilizan la luz a
través de la fotosíntesis como fuente de energía y no requieren de azúcares o
lípidos como fuente de energía. Por consiguiente, el riesgo de contaminación
con otros microorganismos como las bacterias o los hongos es menor en
fotobiorreactores en comparación con biorreactores para organismos heterotroph
INTRODUCCIÓN A LOS BIORREACTORES DE MEMBRANA
Las técnicas biológicas de tratamiento de aguas residuales son muy antiguas y se vienen usando desde hace aproximadamente cien años. De todos los procesos que se han desarrollado para el tratamiento de las aguas residuales el sistema convencional de fangos activados ha sido el más extendido. La tecnología de membrana, en un principio, tenía limitado su uso y solamente se empleaba como tratamiento de afino o terciario en el proceso convencional. La micro-filtración, ultra-filtración y la ósmosis inversa se utilizaron en áreas donde había requerimientos de vertido muy rigurosos o donde se pretendía reutilizar el agua depurada. Los factores principales que limitaron el desarrollo de la tecnología de membrana fueron el elevado coste de inversión y de operación y un inadecuado conocimiento de las ventajas potenciales de las membranas en el tratamiento de las aguas residuales. Sin embargo, con la aparición de módulos de membrana menos costosos y más efectivos junto con el endurecimiento de los requisitos de vertido la tecnología de membrana volvió a cobrar interés.
De forma genérica, los bioreactores de membrana pueden ser definidos como sistemas en los que se integra la degradación biológica de los efluentes con la filtración de membrana (Cicek et al. 1998b).
No sólo se han desarrollado numerosos estudios en plantas piloto sino que en varias partes del mundo hay plantas a escala real que utilizan tecnología MBR (Membrane Bio-Reactors). Los usos actuales incluyen el tratamiento y reciclado de agua en comunidades y edificios, el tratamiento de aguas residuales municipales y el tratamiento de efluentes en determinadas
industrias (Manem y Sanderson, 1996).
Existen varias áreas de aplicación muy prometedoras que están todavía en fase de desarrollo y que requieren una mayor evaluación experimental. Entre ellas se encuentra el tratamiento de efluentes procedentes de actividades ganaderas, aguas residuales de industrias alimentarias, la eliminación de herbicidas y pesticidas de las corrientes de aguas residuales y la eliminación biológica de los nitratos.
Este informe resume en primer lugar la información de varias fuentes bibliográficas sobre los MBR. A continuación se analizan los criterios de diseño para una planta residual urbana. Por último se resumen los criterios de diseño de las membranas de ultra-filtración.
miércoles, 27 de noviembre de 2013
CULTIVO DE CÉLULAS VEGETALES EN BIORREACTORES: UN SISTEMA POTENCIAL PARA LA PRODUCCIÓN DE METABOLITOS SECUNDARIOS
La biotecnología vegetal es un área innovadora y en pleno desarrollo, que ofrece un gran potencial productivo, especialmente si se tiene en cruenta la cantidad de sustancias que producen las células vegetales con aplicaciones medicinales, farmacéuticas, alimenticias y productos de química fina. Las técnicas de micro-propagación y mejoramiento de plantas han permitido desarrollar procesos de producción de compuestos utilizando células vegetales en diferentes tipos de biorreactores.
Los cultivos de células vegetales in vitro ofrecen la posibilidad de producir metabolitos secundarios o realizar biotransformaciones (transformación de un compuesto suministrado exógena-mente) en reactores, en un recinto cerrado o en una planta industrial, sin depender de extensas plantaciones, características de los suelos, condiciones climatológicas e incluso problemas sociales o de tenencia de la tierra. Lo anterior permite incrementar la productividad de metabolitos por unidad de biomasa en biorreactores, con respecto a los cultivos en plantaciones, reduciendo la presión sobre los suelos que están destinados a la alimentación humana y animal. De esta manera, la manipulación de las células vegetales en reactores es atractiva y se convierte en una excelente opción para la investigación y el desarrollo.
METABOLITOS SECUNDARIOS
Actualmente se registran más de 20000 metabolitos secundarios producidos por las plantas y a éste número se suma más de 1600 nuevas sustancias descubiertas cada año (Salisbury y Ross, 1994). Se considera tres grandes grupos de metabolitos secundarios: los terpenos, los fenoles y los alcaloides y de éstos compuestos sólo un número reducido es producido por síntesis química.
TIPOS DE CULTIVO Y BIORREACTORES
Los biorreactores para el cultivo de células vegetales pueden clasificarse en tres grandes grupos dependiendo del tipo de cultivo: células en suspensión, células inmovilizadas y reactores de biopelícula (Kargi y Rosenberg, 1987).
Utilización comercial de reactores con células vegetales.
El primer proceso comercial que utilizó células vegetales fue la producción del colorante y compuesto antibacterial shikonina, utilizando Lithospermum erythrorhizon en 1983.
PROBLEMAS ASOCIADOS AL CULTIVO DE CELULAS VEGETALES
En el cultivo de células vegetales deben considerarse múltiples factores: el medio de cultivo (fuente de C, N, P, K, micronutrientes, hormonas, etc), la irradiación (calidad del espectro, intensidad y período), el esfuerzo cortante (sensibilidad a esfuerzos hidromecánicos, tamaño de las células), el suministro de oxígeno (el efecto en el crecimiento y metabolismo), la composición del gas (e.g. bióxido de carbono y etileno), reología (interacción de viscosidad, mezclado y transferencia de masa con el crecimiento celular y producción de metabolitos en un biorreactos, formación de agregados celulares), el tipo de biorreactor (tanque agitado mecánicamente, columna de burbujeo, airlift, lecho empacado, tambor rotatorio, entre otros), la temperatura, la rapidez de crecimiento e inclusive la variación somaclonal de los callos o cultivos de células (Jain, 2001; Lee, 1996).
Factores que afectan la producción de matabolitos secundarios
Son múltiples los factores que afectan un cultivo de células vegetales y la producción de metabolitos secundarios, ELICITACION Y NITROGENO.
COMPOSICION DEL MEDIO DE CULTIVO
Un medio de cultivo para células vegetales está constituido principalmente por sacarosa, sales inorgánicas -macro y micronutrientes-, vitaminas, fitohormonas.
A una concentración de ion nitrato de 7 mM se presenta un máximo en la producción de shikonina y en la producción de biomasa de Lithospermum erythrorhizon, en un estudio entre 0 y 40 mM. Además, la producción de digitoxina se ve favorecida por una relación de nitrógeno nítrico a amoniacal de 2:1 en un cultivo de D. Purpurea (Collin, 1987). En un cultivo batch de Catharanthus roseus, cuando se presenta una limitación del nitrógeno (tanto nítrico como amoniacal) se presenta una excreción significativa de ácidos orgánicos como el piruvato, lactato, succinato y formato, con la consecuente disminución del pH del medio de cultivo (Bhadra and Shanks, 1997).
www.revistas.unal.edu.co
viernes, 22 de noviembre de 2013
DISEÑO DE BIORREACTORES PARA FERMENTACIÓN EN MEDIO SÓLIDO
BIO-REACTORS DESING FOR SOLID STATE FERMENTATION
En años recientes ha existido un gran interés en los procesos de fermentación en medio sólido por los altos rendimientos que se han obtenido en la producción de metabolitos de alto valor agregado de interés industrial, por lo que se han llevado a cabo investigaciones en el diseño de biorreactores en busca de que sean aplicados a nivel industrial. En el presente trabajo se llevó a cabo una revisión de los principales equipos diseñados para los bioprocesos en cultivo sólido.
Leer más sobre el articulo en:
EL USO DE BIORREACTORES DESECHABLES EN LA INDUSTRIA BIOFARMACÉUTICA Y SUS IMPLICACIONES EN LA INGENIERÍA
THE USE OF DISPOSABLE BIOREACTORS IN THE BIOPHARMACEUTICAL INDUSTRY AND ITS IMPLICATIONS ON ENGINEERING
THE USE OF DISPOSABLE BIOREACTORS IN THE BIOPHARMACEUTICAL INDUSTRY AND ITS IMPLICATIONS ON ENGINEERING
En la industria biofarmacéutica actual, los requerimientos para el diseño de un biorreactor difieren sustancialmente de aquellos de hace 50 años. Hoy en día las nuevas estrategias de cultivo permiten obtener alta densidad celular con altos rendimientos de productos biotecnológicos que deben cumplir con elevados estándares de calidad y normatividad compleja en su producción. Lo anterior obliga el desarrollo de nuevas tecnologías para suplir estas necesidades, por lo que en los últimos diez años el diseño y uso de biorreactores desechables ha crecido de manera exponencial.
Los beneficios de la tecnología desechable son principalmente la eliminación de largos procesos de limpieza, esterilización, calificación, validación, reducción de tiempo entre lotes, el procesamiento de diferentes productos en la misma área, entre otros, lo que conlleva la disminución de los costos que implican esta serie de procedimientos.
Leer mas sobre el articulo en :
EFECTOS DE CORTE EN BIORREACTORES
Los esfuerzos de corte promedio
de flujo laminar no son suficientes para causar daño a la mayoría de los
microorganismos, pero los esfuerzos formados por el rompimiento turbulento del
chorro laminar si lo son. Las velocidades de corte turbulento son difíciles de
definir debido al ángulo variable entre los flujos de las dos posiciones.
Los efectos de corte sobre los
microorganismos han sido los resultados que se resumen en la siguiente tabla.
Correlación para el corte
INVESTIGADORES
|
EQUIPO
EXPERIMENTAL
VOL.(l) IMPULSOR (mm)
|
ORGANISMO
|
INDICACIÓN DE DAÑO
|
CORRELACIÓN
|
Midler y Finn (1996)
|
2.3 50
7.5 100
125
|
Protozoarios (sistema modelo)
|
Rompimiento celular
|
Función
compleja de NDi
No correlacionado por Re o
PN
|
Tanaka et al. (1975a, b)
|
5.0 64
10.0 84
10.0 100
|
Cultivos miceliales varios (por ej. M Javanicus)
|
Perdida de nucleótidos
|
Función lineal
de NDi
No correlacionado por Re o
PN
|
Taguchi et al. (1968)
|
4.5 60
|
Gránulos de L. edodes y A. Niger
|
Fragmentación
Ruptura
|
dDp/dt=kc(NDi)5.5Dp5.7
dn/dt = ktnDp3.2
(NDi)5.7 (NDi)3
|
N= velocidad rotacional del agitador. Di =diámetro del
agitador. Dp=diámetro del; PN= potencia por unidad de vol.; Re=no. De Reynolds; n= no. De paquetes
sobrevivientes; L = longitud hifal media; Kc, kr= constantes.
Estas correlaciones son razonablemente
consistentes en relacionar el corte a una función de velocidad periférica del
impulsor (ND) solamente, aunque la forma de la función varia en el sistema
experimental. La única excepción es el trabajo de Taguchi et al. (1968) donde
el daño también fue función del flujo volumétrico ND3; este parece
ser el caso solamente donde hay fatiga en el suavisamiento del organismo.
Uno de los problemas principales
de este trabajo fue que se llevó a cabo usando depósitos de pocos litros de
capacidad y no hay datos relativos al aumento de escala. La experiencia
industrial ha indicado que la dependencia de la velocidad periférica del
impulsor no se mantiene en cambios a gran escala. Parte de la razón de esto
puede ser que, a escala industrial los agitadores trabajan bajo condiciones
turbulentas, en tanto que este puede no ser el caso a escala del laboratorio.
BIORREACTOR DE MEMBRANA
BIORREACTOR DE MEMBRANA
El Biorreactor de Membranas es un sistema de tratamiento muy compacto por su gran eficiencia de hasta un 95 % y por la poca área que ocupa, ideal para sectores en donde el terreno tiene un precio considerable o en donde una planta de tratamiento e mayores dimensiones puede desvalorizar la propiedad. Este tratamiento combina un proceso de depuración biológica con
una filtración por membrana, la membrana retiene prácticamente la totalidadde los sólidos en suspensión y la biomasa, logrando de esta manera un efluente de gran calidad.
BIOREACTORES CON MEMBRANA INTEGRADA O SUMERGIDA
La unidad de membrana que realiza la separación física está inmersa en el tanque biológico. La fuerza impulsora a través de la membrana es alcanzada presurizando el bioreactor o creando presión negativa en el lado permeado de la membrana.
La limpieza de la membrana se realiza a través de frecuentes retrolavados con agua permeada y aire y ocasionalmente mediante retrolavados con soluciones químicas. Generalmente se coloca un difusor de aire justo debajo del módulo de la membrana para suministrar el aire necesario para homogeneizar el contenido del tanque, para el proceso biológico y para la propia limpieza de la membrana.
MEMBRANAS EXTERNAS O CON RECIRCULACIÓN AL BIOREACTOR
Esta configuración de MBR implica que el licor de mezcla es recirculado desde el bioreactor hasta la unidad de membrana que se dispone externamente a la unidad biológica. La fuerza impulsora es la presión creada por la alta velocidad del flujo a través de la superficie de la membrana.
TRATAMIENTO DE AGUAS RESIDUALES
MEDIANTE UN BIORREACTOR DE MEMBRANA
El tratamiento de aguas residuales especialmente urbanas aplicando la tecnología de Biorreactor de Membrana, comúnmente conocida por sus siglas en ingles como “MBR” (Membrane Biological Reactor); ha tenido un avance muy importante en Europa durante la última década principalmente por la necesidad de muchas instituciones de cumplir con las cada vez más estrictas normas europeas relacionadas con el tratamiento y vertido de aguas residuales.
Fundamento de los biorreactores de membrana
Los Biorreactores de Membranas o Reactor Biológico de Membrana se puede definir como la combinación de dos procesos elementales que son: por un lado un proceso de degradación biológica que puede ser aerobia o anaerobia y un proceso de separación de sólidos y líquidos mediante una unidad de filtración por membrana en el cual los sólidos en suspensión y microorganismos responsables de la biodegradación son separados del agua
tratada.
Biorreactor con membrana externa
En este caso generalmente se coloca un difusor de aire justo debajo delmódulo de membranas para suministrar el oxigeno necesario para el proceso biológico, homogenizando el contenido del tanque yproporcionando
una limpieza a la membrana.
Biorreactor con membrana sumergida
Las membranas deben de limpiarse con periodicidad mediante retrolavado y en ocasiones mediante lavado químico o ambos.
TECNOLOGIA DE MEMBRANAS
Se puede definir membranas como barreras físicas semipermeables que separan dos fases del flujo de entrada, impidiendo su íntimo contacto y restringiendo el movimiento de las moléculas a través de ella de forma selectiva. Este proceso selectivo permite la separación de las sustancias contaminantes del agua, generando un efluente líquido depurado.
TIPOS DE MATERIALES DE MEMBRANA
Principalmente existen dos tipos de materiales que se suelen utilizar, estosson los poliméricos y cerámicos. Aunque también existen membranas de filtros metálicos estos no tienen ninguna relación con el sistema MBR. El material de la membrana debe ser formado (o configurado) de tal modo para permitir al agua pasar por ella.
- Polifluoruro de Vinilideno (PVDF)
- Polietilsulfonas (PES)
- Polietileno (PE)
- Polipropileno (PP)
CONFIGURACION DE LAS MEMEMBRANAS
La configuración de la membrana se refiere a su geometría y la manera
en que esta es orientada en relación con el flujo de agua. El módulo de
membranas define como se agrupan las membranas y permite conocer el
comportamiento del fluido sobre la superficie de esta.
La membrana deberá ser configurada para tener:
- Un área grande de membrana.
- Un alto grado de turbulencia para la promoción de transferencia de
- masas sobre el lado del afluente.
- Un gasto de energía bajo por volumen de agua producido.
- Un precio bajo por membrana en relación al área.
- Un diseño que facilita la limpieza,
- Un diseño que permite la modulación.
USO DE BIORREACTORES PARA
CONTROLAR LA
CONTAMINACIÓN DEL AIRE
INTRODUCCIÓN
Los Biorreactores utilizan un proceso natural tan antiguo
como la vida misma. Para poder Sobrevivir, cualquier ser viviente debe tener
una fuente de energía (alimento) y agua (humedad). La manera en que se usan estas necesidades
para eliminar contaminantes de corrientes de aire contaminadas es el tema de
este reporte.
¿Qué es la biorreacción?
En la contaminación del aire, la biorreacción simplemente es
el uso de microbios para consumir contaminantes de una corriente de aire
contaminado. Casi cualquier sustancia, con la ayuda de microbios, se
descompondrá (desintegrará), dado el medio ambiente apropiado. Esto es especialmente
cierto para los compuestos orgánicos. Sin embargo, ciertos microbios también pueden
consumir compuestos inorgánicos, tales como el sulfuro de hidrógeno y los
óxidos de nitrógeno.
¿Por qué es importante la biorreacción?
En pocas palabras: ¡SU COSTO! El costo de capital de una instalación
por biorreacción es por lo general una mera fracción del costo de una
instalación de un dispositivo de control
Tradicional. Los costos operativos también son generalmente
considerablemente menores que los costos
de la tecnología tradicional. Las unidades de control térmico y catalítico
consumen grandes volúmenes de combustible costoso. Los Biorreactores utilizan
únicamente cantidades pequeñas de energía eléctrica para conducir dos o tres
motores pequeños. Normalmente, los Biorreactores no requieren mano de obra a
tiempo completo, y los únicos suministros operativos necesarios son pequeñas
cantidades de macronutrientes. Los biofiltros, el tipo de biorreactor más
común, por lo general emplean lechos (medios sobre los cuales viven los
microbios) fabricados de materiales orgánicos que ocurren naturalmente (materiales
cortados de parques y jardines, turba, corteza, astillas de madera o abono) que
son consumidos lentamente por la biomasa (es decir, microbios). Estos lechos
orgánicos por lo general pueden suministrar la mayoría de los macronutrientes
necesarios para sustentar la biomasa. Los lechos se deben reemplazar cada 2 a 5
años, dependiendo de la opción de material del lecho.
La biorreacción es un proceso "verde," mientras
que los enfoques tradicionales no lo son.
La combustión de cualquier combustible generará óxidos de
nitrógeno (NOx), materia particulada, dióxido de azufre (SO2) y monóxido de
carbono (CO). Los Biorreactores por lo general no generan estos contaminantes
ni ningún contaminante peligroso Los productos de una biorreacción que consume
hidrocarburos son agua y dióxido de carbono (CO2).
¿Cómo funcionan
los Biorreactores?
Los biorreactores
se han usado por centenares de años para tratar aguas cloacales y otros desechos
olorosos transportados por el agua. Hace aproximadamente sesenta años, los
europeos comenzaron a usar los biorreactores para tratar el aire contaminado
(olores), en particular, las emisiones provenientes de las plantas de
tratamiento de aguas cloacales y las plantas extractoras de grasa. El proceso
inicial utiliza un dispositivo denominado "biofiltro." Un biofiltro es por lo general una caja
rectangular que contiene un pleno encerrado en al fondo, un bastidor de soporte
arriba del pleno, y varios pies de medios (lecho) arriba del bastidor del
soporte.
Se utiliza un ventilador para recoger el aire contaminado de
un edificio o proceso. Si el aire es demasiado caliente, demasiado frío,
demasiado seco o demasiado sucio (con sólidos suspendidos), podría ser
necesario pre tratar la corriente de aire contaminada para obtener las condiciones
óptimas antes de introducirla al biorreactor. El aire contaminado se transmite
a un pleno por medio de un conducto. A medida que fluyen las emisiones a través
de los medios del lecho, los contaminantes son absorbidos por la humedad en los
medios del lecho, entrando en contacto con los microbios. Los microbios reducen las concentraciones
de contaminante al consumir y metabolizar los contaminantes. Durante el proceso
de digestión, las enzimas en los microbios convierten los compuestos en
energía, CO2 y agua.
El material no digerible queda como remanente y se convierte en residuo.

FACTORES QUE AFECTAN EL
RENDIMIENTO:
VARIABLES Y LIMITACIONES
Dado que los biorreactores utilizan cultivos vivos, se ven
afectados por muchas variables en su medio ambiente. A continuación se indican
las variables y limitaciones que afectan el rendimiento de todos los
biorreactores, independientemente del tipo de proceso.
Temperatura
Todas las variables discutidas aquí son importantes. Sin
embargo, la variable más importante que afecta las operaciones de un
biorreactor probablemente es la temperatura. Un chorro de aire caliente puede
matar totalmente una biomasa con mayor rapidez que cualquier otro accidente. La
mayoría de los microbios puede sobrevivir y florecer en un rango de temperaturas
de 60 a 105°F (30 a 41°C) (Ref. 3). Es importante monitorear la temperatura del
lecho por lo menos una vez al día, pero cada ocho horas sería incluso más
seguro. Una alarma de alta temperatura en la entrada de las emisiones también
es una buena precaución de seguridad. Cuando las emisiones provenientes de un
proceso son demasiado calientes, los operadores con frecuencia hacen pasar las
emisiones calientes a través de un humidificador que enfría los gases por medio
del enfriamiento evaporativo. Éste es el método más económico disponible para
enfriar las emisiones de 200 a 300°F (93 a 149°C) a temperaturas de menos de 105°F
(41°C). Además del efecto de enfriamiento, este proceso también aumenta el
contenido de humedad (humidifica la corriente de emisiones), un efecto
colateral deseable.
Humedad
La segunda variable más crítica es la humedad del lecho. Los
microbios necesitan humedad para sobrevivir y la humedad crea la biopelícula que
elimina (absorbe) contaminantes de una corriente de aire, de modo que puedan
ser asimilados por los microbios. Los problemas de baja humedad pueden
corregirse al hacer pasar las emisiones a través de un humidificador. Al tener
emisiones próximas a la saturación (100 % de humedad relativa) resolverán la
mayoría de los problemas de lecho seco. No es necesario que los humidificadores
sean elegantes recipientes de proceso de acero inoxidable, comprados en una
tienda. Pueden construirse de un tanque viejo sobrante de plástico reforzado
con fibra, o bien se puede construir de paneles de fibra de vidrio con una
estructura de madera. El diseño debería incluir varias filas de tuberías cerca
de la parte superior del recipiente, con cabezales aspersores instalados todo a
lo largo, y válvulas de encendido/apagado en cada tramo de tubería para
proporcionar algo de control de la humedad.
Los biofiltros por lo general se operan húmedos, sin agua
corriente ni estancada. Una baja humedad, durante períodos breves, no matará a
los microbios, pero sí reducirá en gran medida la eficiencia. La eficiencia
será menos que la óptima mientras los microbios se recuperan (reaclimatan)
después de un período de condiciones de lecho seco.
Cuidado y alimentación
El nitrógeno es un nutriente esencial para el crecimiento
microbiano. Los microbios utilizan el nitrógeno para construir las paredes
celulares (las cuales contienen aproximadamente el 15 por ciento de nitrógeno)
y el nitrógeno es un constituyente principal de proteínas y ácidos nucleicos.
Los microbios son capaces de utilizar todas las formas solubles de nitrógeno,
pero no todo el nitrógeno está disponible para su reutilización. Algunos
productos de nitrógeno provenientes de los procesos de digestión son gases
(óxidos de nitrógeno y amoniaco), y pequeñas cantidades de éstos saldrán del proceso
junto con las emisiones. No obstante ello, la mayor parte de los vapores que
contienen nitrógeno se reabsorbe en el líquido y es consumido por los microbios.
Además, algunos productos de nitrógeno forman compuestos solubles en agua, y se
eliminan del sistema por lixiviación con agua condensante.
Otros macronutrientes esenciales incluyen el fósforo,
potasio, azufre, magnesio, calcio, sodio y hierro. Puede agregarse nitrógeno,
fósforo y potasio (el código NPK en las etiquetas de los fertilizantes) al
incorporar fertilizantes de uso agrícola en los medios del lecho. Pueden
adquirirse macronutrientes menos solubles, tales como el magnesio, calcio,
sodio y hierro, en pequeñas cantidades en tiendas de venta de forraje y
semillas. El contenido de nutrientes de un lecho.
Acidez
La mayoría de los biorreactores funciona mejor cuando el pH
del lecho es cercano a 7, o neutro. Algunos contaminantes forman ácidos al descomponerse.
Algunos ejemplos de estos compuestos son: sulfuro de hidrógeno, compuestos
orgánicos de azufre, y halógenos (cloro, flúor, bromo y yodo). La producción de
ácidos con el correr del tiempo disminuirá el pH y finalmente destruirá los
microbios. Si un proceso emite contaminantes que producen ácidos, se deberá desarrollar
un plan para neutralizar estos ácidos.
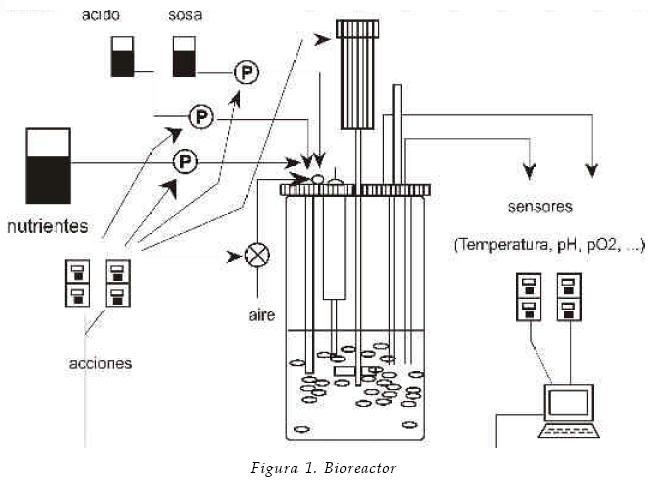
PROCESOS DEL BIORREACTOR
A partir del diseño básico del biofiltro, algunos procesos
nuevos han evolucionado para convertirse en ambiental y comercialmente viables.
Estos nuevos procesos se dirigen a situaciones que no se han afrontado de
manera adecuada en el diseño básico de un biofiltro, tales como la gran
cantidad de espacio requerido, los ambientes ácidos (control del pH), los 8 contaminantes que requieren tiempos de
asimilación más prolongados y la alimentación de los nutrientes.

SISTEMAS DE CULTIVO Y ASPECTOS GENERALES DE BIORREACTORES
Como ya se dijo, el equipo donde se realiza el proceso se denomina biorreactor o fermentados.
El mismo provee todos los servicios que son necesarios para el cultivo, tales
como mezclado, termostatización, suministro de oxígeno, entradas para adición de nutrientes, control del pH, etc. Por otra parte, cuando se habla de sistemas de cultivo o, también, métodos de cultivo, se hace referencia al modo de operar el biorreactor, esto es en forma continua o discontinua.
la información completa de este tema esta en el siguiente enlace
jueves, 21 de noviembre de 2013
BIORREACTOR DE UN TANQUE AGITADO
BIORREACTORES:
el
biorreactor es sin duda uno de los equipos fundamentales de la microbiología industrial.
Es el recipiente donde se realiza el cultivo, y su diseño debe ser tal que
asegure un ambiente uniforme y adecuado para los microorganismos.
El biorreactor de tanque
agitado es de uso muy definido. La agitación se realiza mecánicamente mediante un
eje provisto de turbinas ocasionada por un motor.
ELEMENTOS
DEL BIORREACTOR
Para lograr los objetivos, un biorreactor de tipo de tanque agitado debe contar con las siguientes composiciones:
Cuerpo
del biorreactor: recipiente o contenedor que alberga el
cultivo o microorganismo. El contenedor es la frontera física entre el ambiente
externo y contaminado y el ambiente interno controlado.
Dimensionamiento del Cuerpo del Biorreactor: el primer paso en el diseño de cualquier biorreactor es dimensionar el “tamaño” del tanque o del cuerpo del biorreactor; la práctica común es, hacerlo a través de variables adimensionales: variables que representan una razón entre dos parámetros con las mismas dimensiones. De esta forma, es posible escalar; es decir cambiar de dimensión o tamaño, el biorreactor y adaptarlo a otra escala de proceso.
Eje trasmisor de la potencia:: es una barra cilíndrica de acero inoxidable 316L y por lo general se diseña en diámetros estándar: ¾”, ½”, etcétera para mayor facilidad de ajuste a los estándares de motores a.c. Su longitud depende de la profundidad del contenedor (tanque).
Dimensionamiento del Cuerpo del Biorreactor: el primer paso en el diseño de cualquier biorreactor es dimensionar el “tamaño” del tanque o del cuerpo del biorreactor; la práctica común es, hacerlo a través de variables adimensionales: variables que representan una razón entre dos parámetros con las mismas dimensiones. De esta forma, es posible escalar; es decir cambiar de dimensión o tamaño, el biorreactor y adaptarlo a otra escala de proceso.
Eje trasmisor de la potencia:: es una barra cilíndrica de acero inoxidable 316L y por lo general se diseña en diámetros estándar: ¾”, ½”, etcétera para mayor facilidad de ajuste a los estándares de motores a.c. Su longitud depende de la profundidad del contenedor (tanque).
Acople del Eje Transmisor: ajusta y
fija al motor, el eje transmisor de potencia.
Existen dos tipos de acople:
Acople-adaptador de tipo
taladro el puerto de entrada se acopla al eje del motor por fijación directa.
El puerto de salida es un dispositivo que se adapta a varios diámetros de broca
y sujeta o abraza firmemente el eje transmisor de potencia por presión y
abrasión; similar al que utilizan los taladros mecánicos.
Acople-ajustador de tipo
tornillo-rosca el puerto de entrada se “enrosca” o se fija
firmemente al eje del motor. El puerto de salida es un dispositivo que “abraza”
el eje transmisor de potencia por un mecanismo de tornillo-rosca.
Flujo axial:
suministran mayor efectividad de mezclado (distribución) y reducen la potencia
de mezclado requerida, al distribuir mejor la mezcla; sus hojas u aspas son
planas.
Flujo radial: generan
mayor potencia de mezclado (turbulencia) y pueden causar daño celular; sus
hojas o aspas son del tipo hélice.
Impulsores: son los
dispositivos que impulsan el fluido y el movimiento, mediante hojas o aspas
unidas al eje transmisor de potencia; pueden ser del tipo mecánico (agitador) o
hidráulico (turbina).
Agitadores: es un
impulsor formado por hojas o aspas de agitación conectadas al eje transmisor de
potencia; pueden tener una distribución de flujo axial o radial.
Turbinas: es un
impulsor de flujo axial el cual opera como una centrífuga que distribuye el
flujo de líquido a través de hojas planas, a todo el volumen de fluido.
Puerto de Entrada del Biorreactor: se denomina puerto a la superficie física sobre
el cual se instala un dispositivo de entrada o salida al biorreactor, un
anclaje o un aparato mecánico o de medición; el puerto es el medio por el cual,
se ajusta o fija, tal dispositivo o artefacto a la pared o superficie del
tanque o del biorreactor.
Sello Mecánico: su función
es triple: evitar la contaminación, mantener hermético el sistema, servir de
amortiguador de fricción. El sello mecánico también debe permitir la
esterilización in situ del biorreactor, mediante una línea de vapor sobrecalentado.
Un sello mecánico, generalmente se diseña en una de dos configuraciones:
Cartucho rígido: que
permite el rodamiento del eje de potencia a través de soporte de cuerpo rígido
que sella y aísla el paso de cualquier materia al interior del depósito.
Cartucho flexible: que
permite el rodamiento del eje de potencia a través de un soporte fijo al
exterior pero flexible en el interior y que también sella y aísla el paso de
contaminantes al interior del depósito.
Sistema
de agitación: tiene la función de generar la potencia
necesaria para producir una mezcla perfecta para el sistema de cultivo y
producir un régimen de agitación adecuado.
Motor
impulsor: motor de inducción dado que un biorreactor debe operar de
forma continua durante todo el proceso de cultivo, se requiere un motor capaz
largos periodos de operación continua y trabajo duro por eso el motor debe ser
de inducción de corriente alterna y debe ser acorazado, preferiblemente de
acero inoxidable.
SISTEMA
DE CONTROL
Control de velocidad del motor : los motores de inducción de corriente alterna tiene velocidades nominales a rotación de 1800rpm o 3600rpm. Estas velocidades son muy altas para los sistemas biológicos causando la destrucción de las células y microorganismos en cultivo.
AGITACIÓN Y MEZCLADO
Relaciones de Potencia y Mezclado: conforme el diámetro de la hoja o aspa (Dd)
aumenta, también lo hace, la potencia (Pt) requerida para realizar el trabajo
de mezclado; la potencia de mezclado (Pm) es mayor porque el torque (τ) se
acrecienta, recuerde que el torque es la relación entre la fuerza (F) y el
brazo de palanca (r) y que, el brazo de palanca es el diámetro del aspa u hoja
cuyo momentum (mv) aumenta al aumentar la velocidad de rotación (ω).
Utilización de Bafles: son una mejora muy utilizada ya que pueden
instalarse fácilmente en los sistemas de agitación, disminuyen (deflectan) la
turbulencia ocasionada por las hojas o aspas del impulsor, rompen (disgregan)
los cúmulos celulares y micelios que se forman en los respectivos cultivos y
mejoran la eficiencia de mezclado.
REACTOR DE TANQUE AGITADO O RTA
Son los que cuentan con un agitador eficiente para lograr que la composición y la temperatura de la masa reaccionante tiendan a ser iguales en todas las zonas del reactor, es decir lograr una uniformidad de las propiedades. El diseño del agitador y su velocidad puede afectar las condiciones de mezclado. A esta Categoría pertenecen los reactores de empleo más común en la industria química. La mayor parte, esta equipado con algún medio de agitación (centrifugación, oscilación o sacudidas), así como elementos para la transferencia de calor (intercambiadores de calor de cubierta, externos e internos). Esta clase admite tanto la operación intermitente como la continua en amplias gamas de temperatura y presión. Con excepción de los líquidos muy viscosos, el reactor tanque con agitación produce un mezclado casi perfecto (retromezclado).
SISTEMA
DE DIFUSIÓN DE OXÍGENO DISUELTO
Debe optimizar al máximo la
transferencia de oxigeno disuelto al medio liquido. El sistema consta de dos
partes mecánicas: boquilla y difusor de aire;
Una parte de medición;
sensor de oxigeno disuelto y una de control controlador de oxígenos disuelto.
Difusor
de aire: los cultivos aerobicos requieren que la corriente de aire
esteril se difunda en la forma de miles de pequeñas burbujas, desde el difusor
de aire hacia el volumen del liquido.
Control
y medición del oxigeno disuelto: además de regular el flujo y
la presión de aire en la línea o tubería, se debe controlar el valor y la concentración
de oxigeno disuelto dentro del medio liquido.
http://es.scribd.com/doc/31787823/Biorreactor-de-tanque-agitado-Morgan-G-Vasquez-2010
http://es.scribd.com/doc/31787823/Biorreactor-de-tanque-agitado-Morgan-G-Vasquez-2010
http://cursa.ihmc.us/rid=1HWW5NT4D-1TK1SKD-N9Z/Dise%C3%B1o%20de%20un%20Biorreactor%20de%20Tanque%20Agitado.doc
https://www.google.com.co/#q=+biorreactor+de+un+tanque+agitado&safe=active
Suscribirse a:
Entradas (Atom)